The experiences of David Parsons and F24 ‘Gypsy’.
I am writing this article to pass on experiences and tips that I have learned from maintaining the decks of Gypsy, my Finesse 24. I do not profess to be any sort of expert in this area- more an enthusiastic amateur.
Looking back I probably should never have bought Gypsy. I was looking for a renovation project but, with hindsight, the challenges that I was about to face were beyond my skills in terms of woodworking, and beyond my knowledge in terms of the construction of the boat. However, on the plus side, her hull was in great condition and I managed to negotiate a price that I felt was fair- and left me with enough money to replace all of the “expensive” items: the sails, cushions, engine etc. Finally, I really wanted this boat.
So, undeterred, I arranged for the boat to be transported to a boatyard in Benfleet, Essex where I set about the renovations with my son (who is the co-owner of Gypsy).
I had probably spent too much time concentrating on the rather frightening cracks (I now refer to these as “shakes” with my newly acquired expertise!) in the cabin sides and hadn’t really appreciated the extent of the rot in the decks. Too late now, so we set about excavating the damaged areas.
The majority of rot was:
- At the edges where the deck abuts the cabin side. This had occurred because the seal established by the quadrant moulding had broken down and water had permeated into the edges of the ply.
- At the edges where the deck meets the rubbing strake. This had most likely occurred from overzealous sanding that had broken down the fibreglass matting, again, allowing the water to seep into the ply.
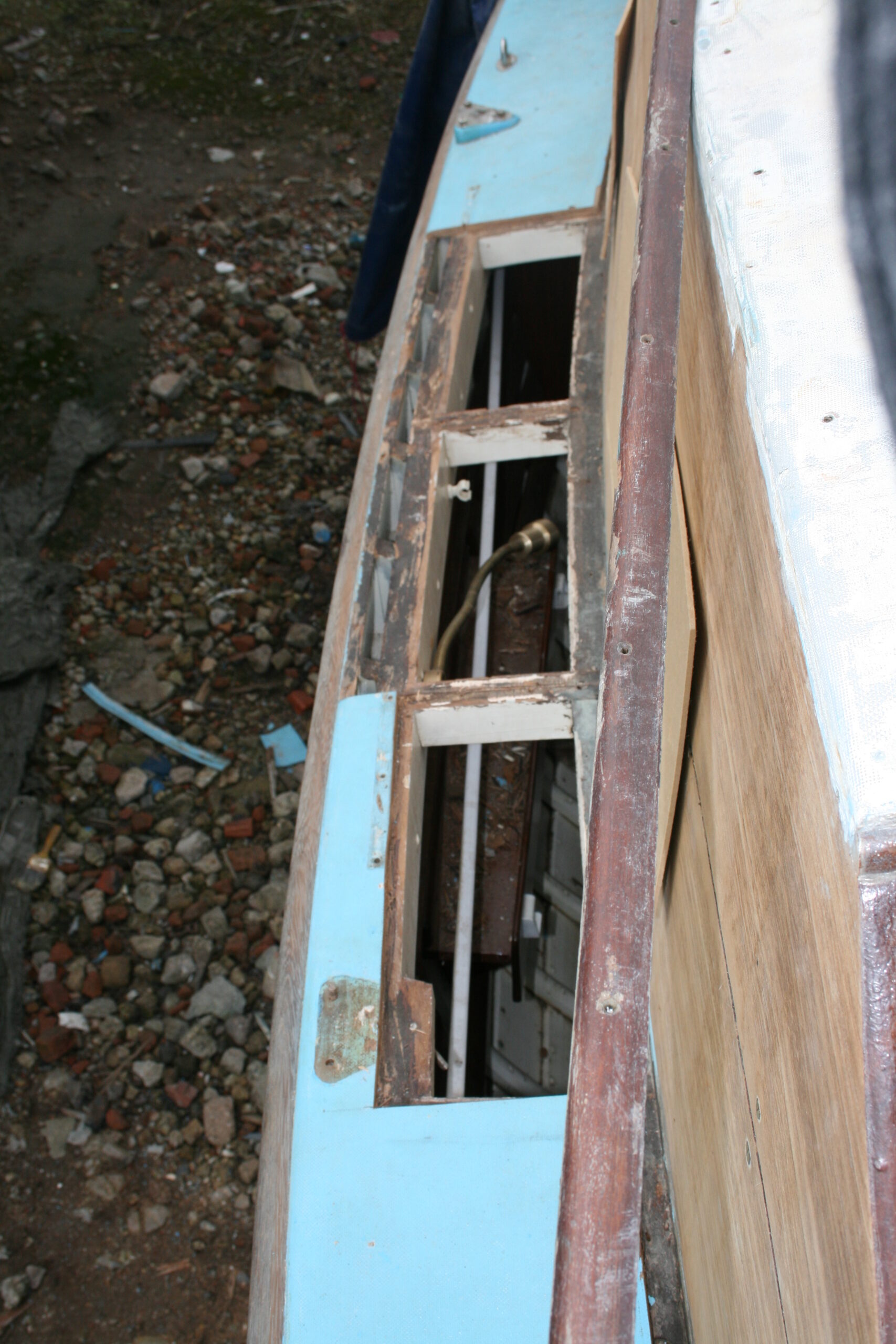
Cutting back the rotten decks and finishing along the deck beams – Gypsy
- Behind the cockpit where movement of the main sheet horse, probably through people leaning on it, had broken down the seal with the deck covering where the horse is bolted through the deck.
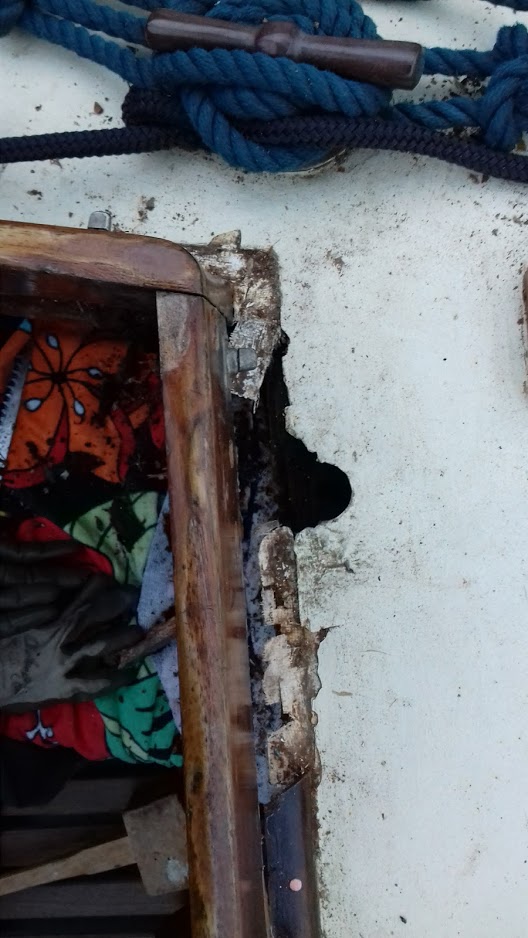
Evidence of rot around the mainsheet horse fixing – Calluna
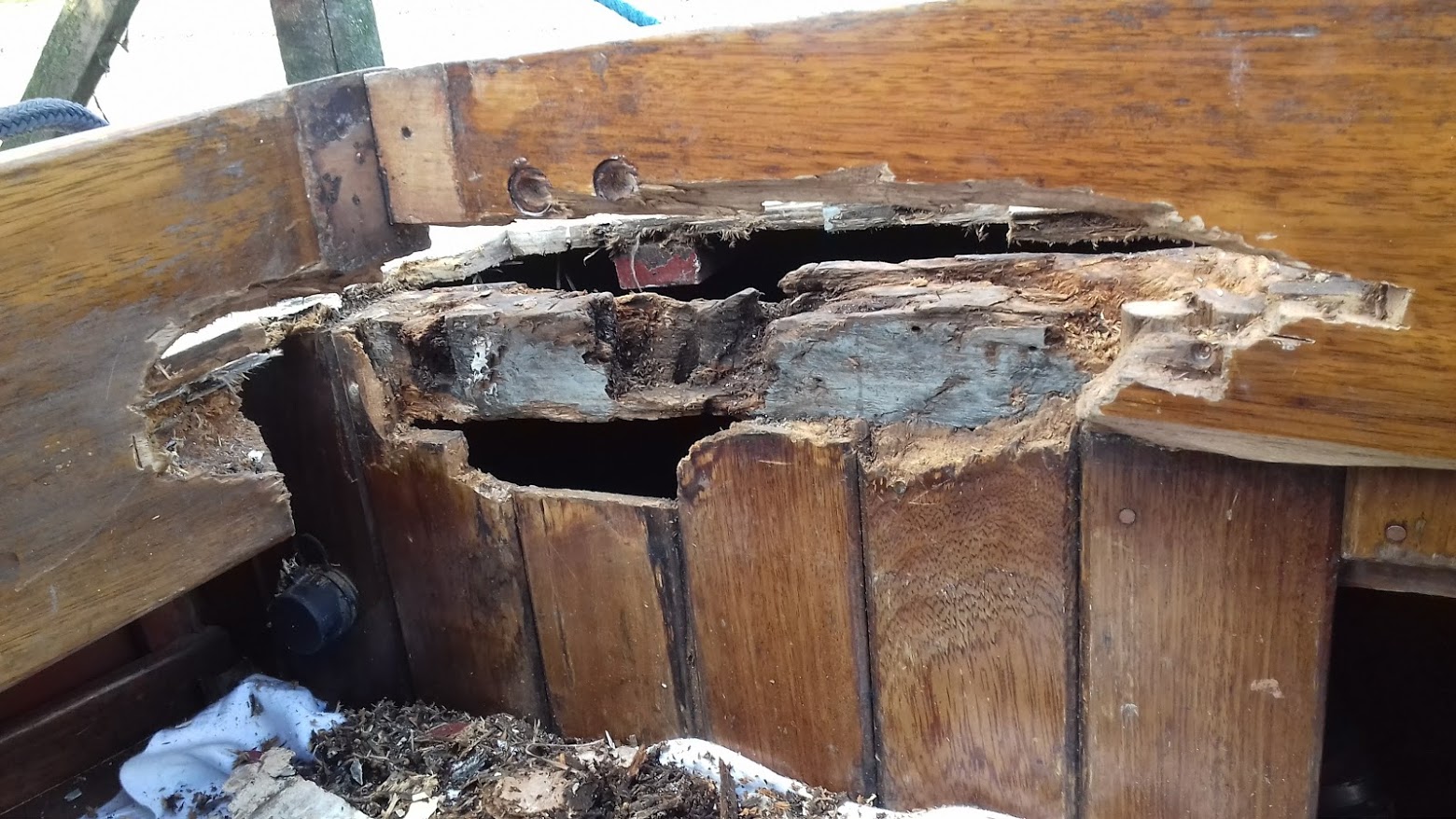
Extent of the rot caused by the mainsheet horse fixing leak – Calluna
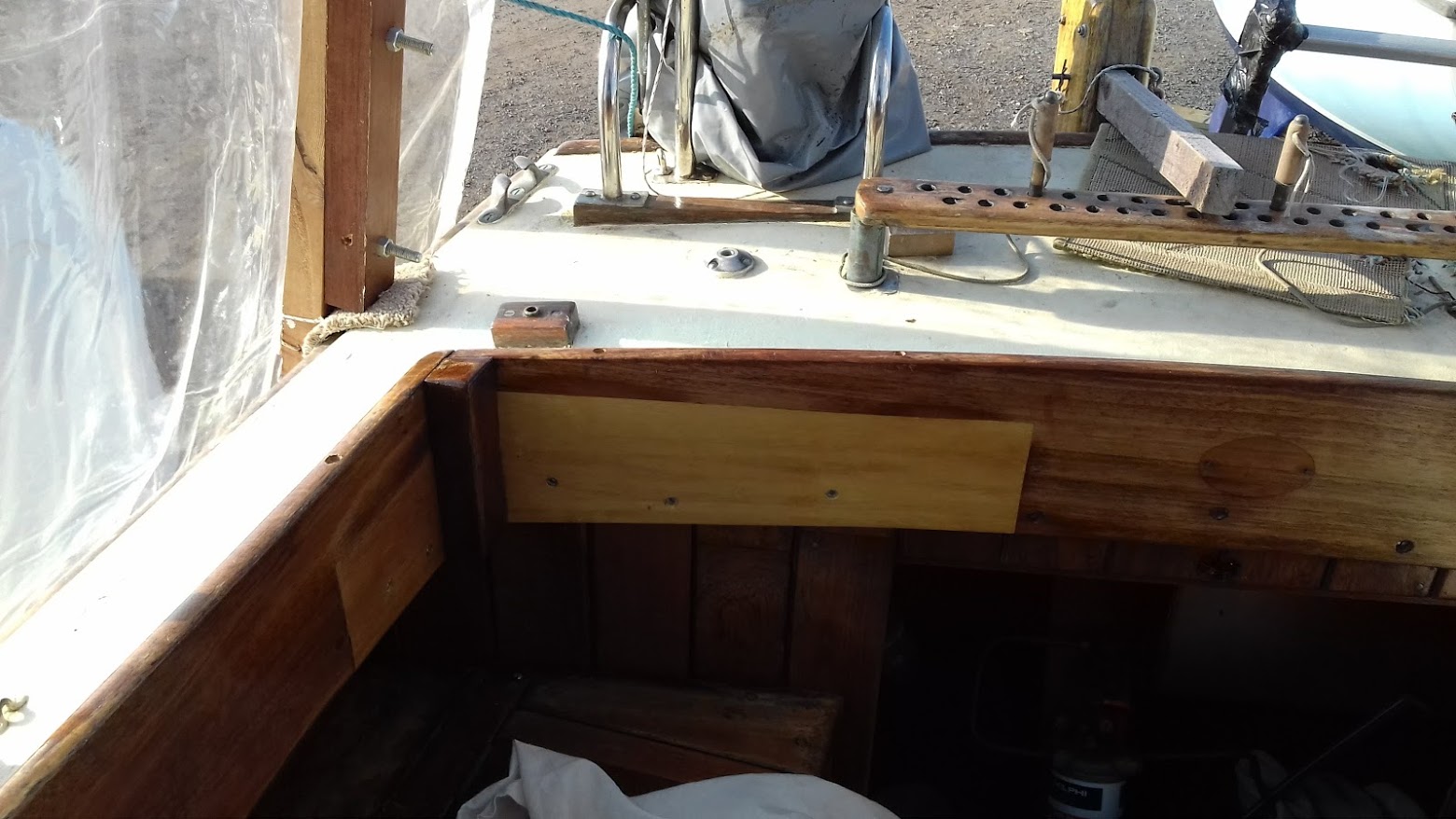
The final repair job – Calluna
Finally, a small amount of rot was uncovered in the top of some of the deck beams and in one area of the top plank and rib of the hull, all of which were conveniently hidden under the decks. Fortunately these could be easily repaired by cutting back, scarfing and gluing in new wood sections.

Cutting back the rot in the top plank and rib – Gypsy
We removed all of the quadrant moulding at the base of the cabin sides. Interestingly, we noted that the fibreglass matting had been lapped up about a centimetre onto the cabin sides. We expect this was to establish a seal but quite a lot of this had broken down, possibly by the natural movement of the wood over the years.
Using an oscillating multi-tool, ideal for this job, we started cutting back the rot. With hindsight, we were overcautious with our cutting back and were left with decks peppered with square and rectangular holes with cuts aligned with the underlying deck beams allowing a firm fixing point for our new ply. We were probably in too much of a rush to start repairing the holes and should have been a lot braver and cut out larger areas from the cabin sides to the gunwales. This would have enabled us to reduce the number of joints in the ply and matting resulting in an easier and neater job that may have lasted a lot longer.
Given the extent of the rot our second mistake was not removing the rubbing strake or large lengths of it. We did consider doing so, but it was not damaged and we were anxious that we would, more than likely, create more damage by trying to remove it. The reason it is preferable to remove it is that re-laid matting can be brought down over the edges of the deck ply and finished behind the rubbing strake, creating a watertight seal. I have since seen that the rubbing strake can be relatively easily removed by drilling out the wooden plugs and unscrewing it from the hull. No glue was used on Gypsy to fit this on the original build.
As we did not remove the rubbing strip we routed the curve on the edge of the ply to match the remaining deck edge and laid the matting down to the top of the rubbing strake wetting it down with plenty of epoxy. Leaving the rubbing strake in situ is not the ideal repair as there is always the chance that water can permeate between the matting and the top edge of the rubbing strake. A better way would have been to terminate the square edge of the ply back from the edge of the deck and create a hardwood edging strip that could be epoxied to the ply and then matted and epoxied over. This would avoid the cut edge of the ply being vulnerable to further damage and water ingress over time.
Back to the repairs: before refitting the new ply we thoroughly epoxied the replacement sections and edges of the new and the old ply. At the time we used 12 mm ply but we have since realised that two layers of 6mm ply would have made the job far easier in terms of flexibility. We fitted the new ply down with countersunk stainless steel screws and epoxy filled all of the screw heads and the small gaps between the old and new ply.
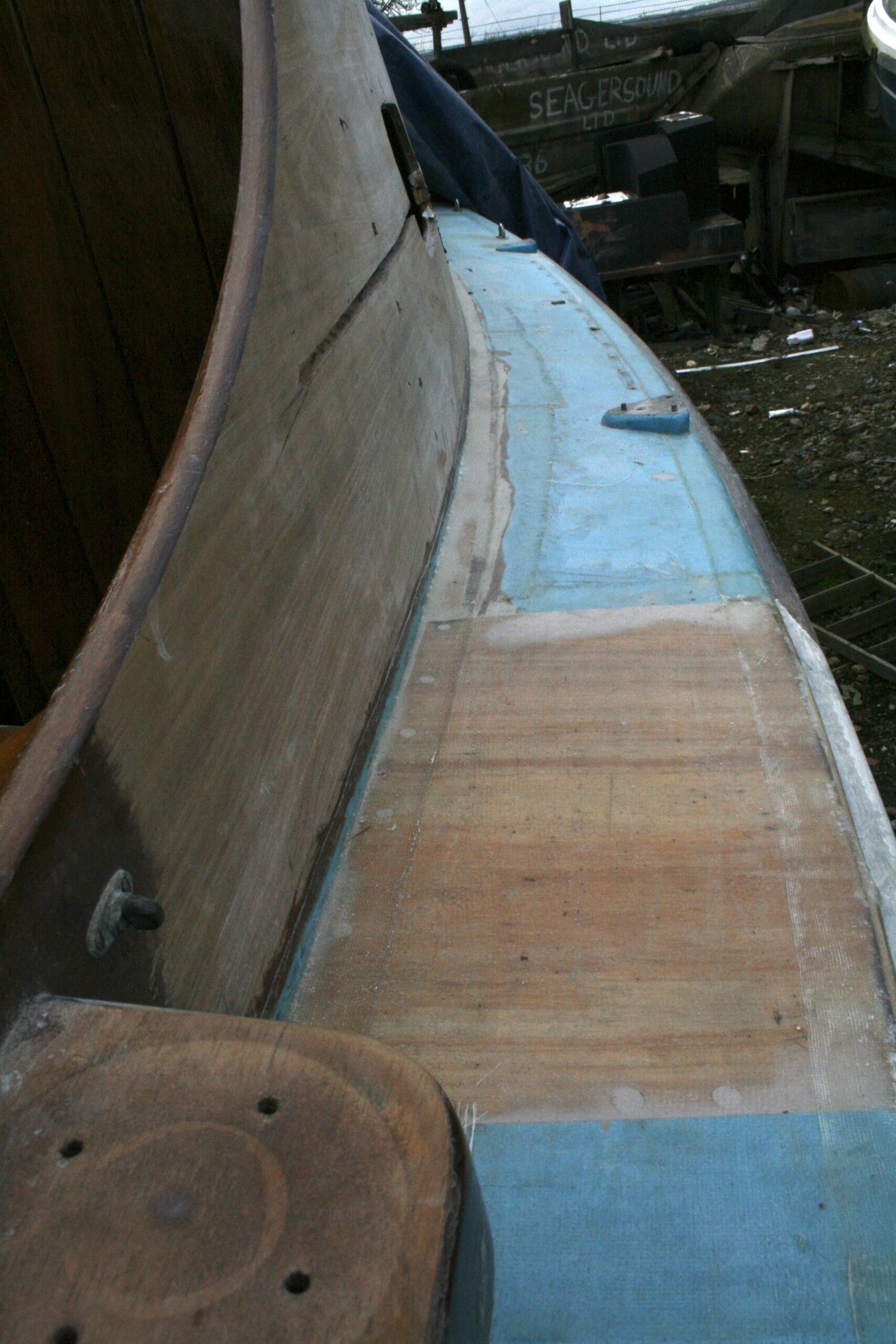
New deck fitted, filled and matting epoxied ready for finishing – Gypsy
When the original decks were laid they were fixed with galvanised nails; I understand that bronze nails were considered an “extra”. A common problem is that, over time, the nails rust, bleed through, and break down the deck covering. To prolong the deck life it is advisable to nibble the area above the rust marks to expose the errant nail head , tap it down a few millimetres , treat it with a rustproof paint, and fill and fare with epoxy filler. Had the original nails been tapped down and filled over this may have prevented this problem
The most difficult replacement deck strips to fix were along the edges of the side decks. This is because there is a gap of about an inch between the top plank of the hull and the longitudinal deck bearers. Again, we have since realized that we could have made a better job by letting a strip of hardwood into this gap and attaching it to the longitudinal deck beam. This would have created a far better fixing for the deck edges.
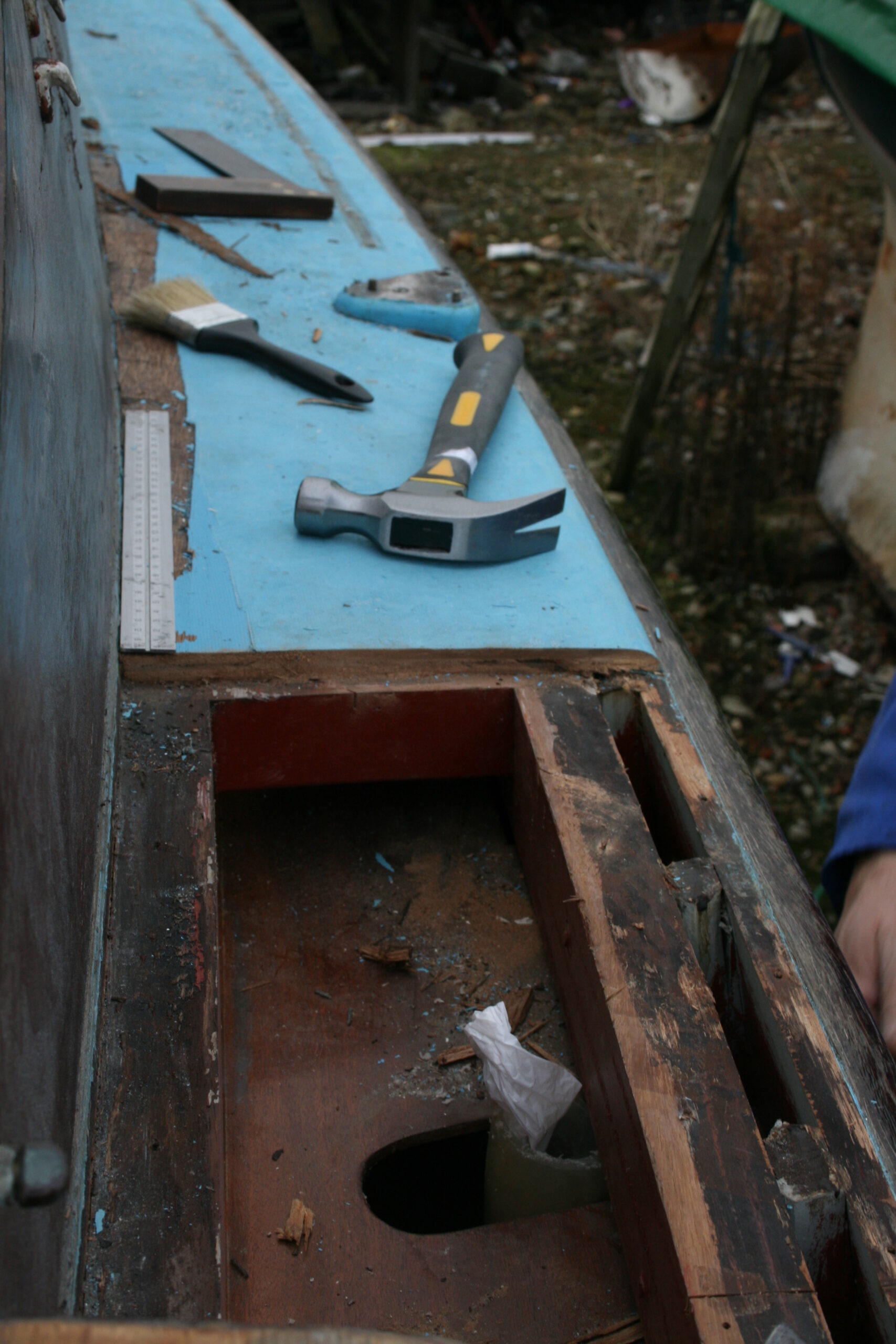
Note the gap between the top plank and deck beam where the addition of a hardwood infill would improve the fixing base for the deck edges- Gypsy
The postscript to this article is that our repairs, with all their flaws, lasted about eight years. We then noticed that soft areas were beginning appear in other areas of the deck. To be frank, there is probably a point of no return with deck repairs when the patched areas exceed the area of the original deck. So we bit the bullet and had all of the decks professionally replaced by J Star Marine Services at Walton on the Naze. He did a great job and it was watching this work that led to some of the repair tips mentioned above.
The unexpected bonus was that, as well as having new solid decks the rather musty smell we had been used to in the cabin had now gone.

New decks fitted and the first coat of deck paint applied. Note the matting overhang upon which the rubbing strake is fitted – Gypsy
So, what lessons have we learned? Firstly, we should have looked at more F24s. They regularly come onto the market and the condition of the boats varies widely; we could have saved ourselves a great deal of work by paying more for less of a ‘project boat’. You live and learn.
To conclude, after a succession of fibreglass boats we were looking for a classic wooden boat suitable for the East coast and we have not been disappointed. For the price she is the perfect boat for our requirements and provides hours of fun either sailing, improving your woodworking skills, or pottering around on the mooring.